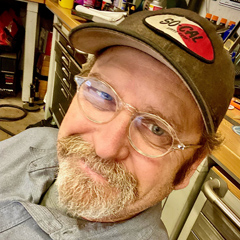
Crimping on New Battery Terminal Connectors
Mark SimpsonDescription
You know, when you working on classic cars, they don't always have, you know custom say made battery cables for them, or you wish to, you know, maybe relook, you know, in performance car it takes a common thing to relocate the battery to the trunk. You get move all that weight all the way back to over your rear axle so you can get better traction. And so there's a number of reasons why you may need to build your own battery cables. You know, you can get, you know this is about the heaviest you'll use. Now, automotive is the two hot wire, you know you'll use this if you're putting, you know, your battery way back in the trunk, because you'll need, you know the extra size to cover the distance from your starter to, you know, your battery, so you need a good heavy wire, but putting terminals on wires, like this can be a challenge.
You know, you could go in and cut this cable and solder this on, I don't like soldering them on so much because what happens is you have to get a good bond with your cable, you have to put so much heat to this, that you end up you know, melting back here, insulation some. So we're gonna look at the process to cut the wire and then crimp the new terminal on here using a lug crimper. To start, we're gonna use just a, a heavy duty cable cutter and, you know, you could cut this with a, you know, if you've ever tried it with a hacksaw or you can cut it with a hacksaw or a chop saw or anything else, but you know, the cable cutter really make short work of of cutting copper cable. And it does a nice job at same time. So you get a nice clean cut quickly and easy without a lot of hassle.
Once the cable is cut, you know, we need to strip back this insulation and we need to strip it back you know, about, you know, half inch or so. So just grab, you know, we'll just grab our pocket knife here and just kind of follow it around, make a, make a cut in the sheathing Without, you know, wrestling this, wrestling this heavy cable can be a little bit of a challenge but it, it's nothing that you can't expect then after you make the cut all the way around you can just kind of cut it up. You really wanna make sure you get a good cut all around on the insulation. It it's got good, heavy insulation on it. Okay, now that we've got our cable exposed we're ready to put our end on here, and, this type of lug crimper is, you know, this this is one type of lug crimper and there's probably, you know, several different kinds, some, you know, actually use a couple of dyes that prescient from both sides.
This is a, this is what I call a dimple crimper because it has a V shape on one end and then a dimpler that comes in and presses this into the, the housing itself. So the best way I've found to do this is just kind of set it up. I always put the, the dimple on the bottom side you can see where the lug is, is a a kind of position so this would be the top where you'd bolt this up against something. And the dimple itself would be in the bottom, insert the cable, make sure you have it in there good and just the matter of pressing down on the lever and this one is adjustable. So we've already set it up for this size connector And you can see where it's actually forced this in.
We have a good solid connection now so we know this cable has a good connection. The last thing I like to do is put a piece of shrink tube on here, what this does is this help seal this up so I don't have to worry about getting any moisture in here. And there's the completed cable. As you can see it with the right tools, we can put an end on a battery cable, have a solid watertight connection in just a matter of minutes.
Every time I watch a video related to electrical or wiring from these guys, I am glad I only paid $2 for a membership. The guy seems like he's trying to be helpful but generally ends up showing how not to do wiring. It's painful watching some of these.
Kind of a bogus way of stripping the cable with a Leatherman type multi tool? Why not use a cable stripper. And use a hydraulic crimper with dies to get an even crimp all the way around. Glad to see you used heat shrink. Sorry, Not impressed with the professionalism.
When he has a birthday buy him a tape measure that is more like 3/4 - 1 " he is stripping back.. While you are playing with nice tools they make a nice tool for cutting and stripping the insulation that doesn't make a mess of the wire
sorry, but that wouldn't cut it here(nice to see the heat shrink tubing to cover up the poor workmanship). Use dies but if one wanted to use solder, you would put the terminal in a vise,m heat it up, add solder , and THEN while it's still fluid, push the wire into it--this will NOT ruin the wire wrap(then put your heat shrink on). Better yet is to use crimp dies; you want to get the outside of the copper wires unexposed to air; (the electrons/conductivity runs mainly on the outer surface of the copper, not inside it)
I would use a little No-Ox on the cable before I crimped on the lug.
Still trying to build my 59 300E Ford Thames Van