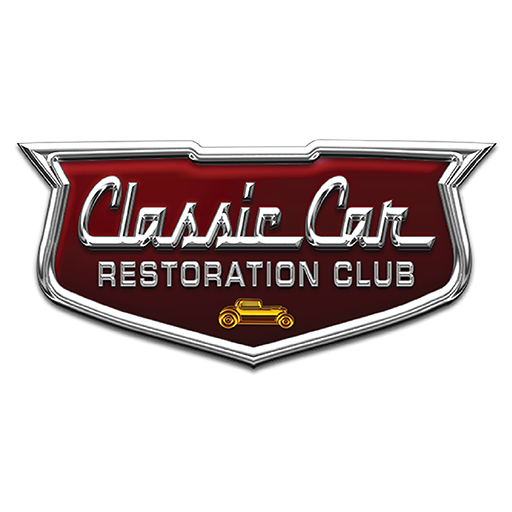
Design and Build a Sheet Metal Jig
Classic Car Restoration Club EditorsDescription
With the advent of the Industrial Revolution and the rise of mass production techniques in the early 20th century, the need for increased efficiency and standardization became apparent. The use of jigs and fixtures emerged as a solution to achieve consistent results in sheet metal forming. Jigs, often made from wood or metal, were created to guide and support the metal sheets during the forming process, ensuring accuracy and repeatability.
Automotive manufacturers played a crucial role in advancing the use of jigs for sheet metal forming. As the demand for automobiles grew, manufacturers sought ways to streamline production and reduce costs. Jigs became essential tools in this process. Companies like Ford, General Motors, and Chrysler invested heavily in research and development to improve the efficiency of their sheet metal forming operations.
Over time, the materials and techniques used in jig making evolved. Wood was gradually replaced by metal, offering greater durability and precision. Welding and machining technologies advanced, allowing for more complex and intricate jig designs. Additionally, the use of computer-aided design (CAD) and computer-aided manufacturing (CAM) systems in recent decades has revolutionized jig making, enabling faster prototyping and more efficient production processes.
Current metal stamping and assembly techniques have eliminated the need for craftsmen to labor for hours shaping and assembling intricate panels; many of these “Old School” techniques are still utilized today by Classic Car Restorers. We joined up with Bruce Macleod of the Contour Autocraft Academy to learn how to create sheet metal forming jigs and understand how they are used in the fabrication process. Bruce explains the Importance of using a jig to accurately duplicate a double curvature panel. He further explains common problems encountered while fitting and shaping panels.
Macleod explains how to build a profile gauge of a panel, and working from a “Datum Line” along the crown of the panel, create accurate ribs or crocs plates of the panel profile. He shares some important tips to accurately scribe a new profile template and trim and weld several segments together.
He also explains the best practices for building and assembling the jig and important considerations for clamping and using the jig. Finally Bruce explores the different materials and hardware that can be used in a jig, including incorporating hammer forms on the jig to aid in forming tight curves directly on the jig.
If you’re serious about metal fabrication on classic cars, sooner or later you’ll need to build a jig. This helpful video will get you off to a great start and ensure the panels you make or repair fit accurately to the original contours.