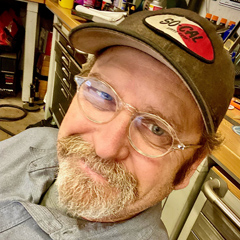
Panel Bond Rocker Panel Replacement
Mark SimpsonDescription
Unlike welding, which involves high heat, panel bonding does not introduce excessive heat into the panels. This reduces the risk of distortion or warping, which is particularly important for classic cars with delicate sheet metal. In addition, the adhesive used in panel bonding offers excellent corrosion protection. This is essential for preserving the integrity of classic cars, as rust can be a significant issue. Panel bonding results in a clean and seamless finish, as there are no visible weld seams or rivets. This is especially important for classic cars where aesthetics are a key consideration.
But the benefits of panel bonding don’t end there, modern panel bonding adhesives are designed to provide a strong and long-lasting bond. They are often formulated to withstand the stresses and vibrations experienced by a vehicle. It can also be used for a variety of materials, including steel, aluminum, and composites. This versatility makes it suitable for various classic car restoration projects. Panel bonding is often quicker than traditional welding or riveting methods, making it a more efficient choice for some restoration projects.
Here’s a quick summary of the process of using panel bond:
Surface Preparation: Before applying panel bond, it’s crucial to prepare the surfaces properly. This typically involves removing any rust, paint, or contaminants from the metal. The goal is to create a clean, bare metal surface for the bond to adhere to.
Panel Bond Application: A two-part epoxy adhesive is applied to the mating surfaces of the panels. The adhesive is often dispensed through a caulk gun or specialized applicator.
Panel Alignment: The sheet metal panels are carefully aligned and positioned according to the desired fit. Proper alignment is essential for a neat and precise result.
Clamping: To ensure a strong bond and maintain the alignment during curing, clamps are used to hold the panels together while the adhesive cures. The curing time can vary depending on the specific adhesive used, but it typically takes several hours to a day.
Excess Adhesive Removal: Once the adhesive is fully cured, any excess adhesive that may have squeezed out from between the panels is removed. This step ensures a clean and professional finish.
Finish Work: After the panel bond has cured and the excess adhesive has been removed, the area can be sanded and refinished to achieve a seamless appearance. This may involve applying body filler, priming, and painting the panels.
Old habits die hard and when Mark Simpson needed to replace the rusted out rocker panels on the shop truck Gary Simpson volunteered to guide us through the process of using Panel Bond to replace them instead of welding. Mark admits, the ease of installation and the strength of the final result surprised even him, making this one of the preferred methods for attaching sheet metal panels on classic cars due to its many benefits, including reduced heat distortion, corrosion protection, a clean appearance, strong bonds, and versatility. When performed correctly, it can help preserve and restore classic cars. Follow along as we transform the shop truck with some new skins.