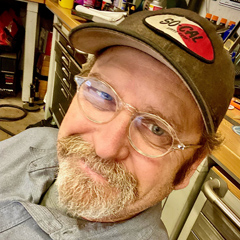
Powder Coating Process: Tips and Techniques
Mark SimpsonDescription
[Announcer in blue] Hello and welcome. My name is Jeffrey Larson. And today I'm in the shop with Mark Simpson, managing editor of Classic Car Restoration Club. Today, we're going to be doing some powder coating with a kit from Eastwood. This kit features a dual voltage power gun their oven, their powder, silicone plugs and high temperature masking tape.
So Mark, what parts will you be powder coating today and from what car? Today we're going to actually be working on a master cylinder for this car. For this 57 DeSoto. And the reason we're doing the master cylinder is because you can't really paint the master cylinder. Because the brake fluid will take off the fluid.
It's a good subject to powder coat because the powder coating actually will resist brake fluid. And keep this looking really nice up on the firewall where everybody can see it. So what are some of the benefits of powder coating versus just painting the master cylinder? Powder coating is a, is a great product because it has a lot of advantages over paint. It's more scratch and scuff resistant.
Another thing that's a good is it's environmentally friendly. You know basically. We're taking a powder that is a thermoset plastic just a ground plastic. And we're adhering this to the surface of the product that we were going to be working on. And then it's baked at 400 degrees and it actually fuses to the surface and cross-links to itself creating a really hard durable finish.
So we don't have to worry about it coming off like a paint would. Thanks, Mark. That sounds great. I'm going to get out of your way, let you get started. And I'm really anxious to see what the parts look like when you're done.
Super! Thanks Jeffrey. The prep for powder coating apart is no different than prepping apart for paint. And so we want to make sure that the surface is clean, oil-free. And the last step is, we're going to prepare this by actually spraying it down with some paint prep.
And it shouldn't matter, hosing it down and then wiping it off. And just like paint prep, the more time you spend actually getting it clean and making sure your surface is, is well-prepared; it will pay off in your final finish. The next thing we'll do is actually plug our line ports. And to do that, we'll use the silicone plug. The advantage of the plugs is that they actually will seal the holes and prevent any powder from getting in.
As well as they're heat resistant and can actually drop them right into the oven. Without concerns about melting while we're going through the powder coating process. Now that we have the holes plugged, we're ready to seal off the top of this. And to do that, we'll be using the Eastwood's fiberglass tape. Again, the real advantage of this tape is it will take the 400 degrees that it's going to be subjected to in the oven.
And will keep powder from getting any place that we don't want it. We'll start by taping off this edge. Okay, next to fill in the big hole here in the middle. We'll just be using like regular household aluminum foil. We want to make sure there's no tape, of course.
Hanging down into the places that we want to make sure we have coated. And we'll use our knife to trim that up nicely. Last thing that we really need to seal up is the backend of this cylinder bore for a master cylinder. How we're going to do that is a little different. What we're going to do is I've taken a large rubber grommet and I've taped it to our grounding rod.
And what this will do is when the master cylinder is pressed up against it, form a seal without having to take that whole off. This will give us a way to suspend it while we're actually powder coating it. With that we're going to wipe it down one more time with our Eastwood paint prep. It's a good idea to, you know keep your finger oils away from the part at this point. This will ensure that none of your your finger oils will affect your powder.
And give you a good coating when you're done. What we'll be using today is a semi-gloss powder. And what that is, is it's a black that will have kind of a semi-gloss sort of a factory sheen to it. You can get clears. You can get transparent colors as well as really bright opaque colors.
And there's a good variety. The thing you can't do is mix colors together. I know with like paints and stuff that you could mix like a yellow and blue together and have a green. With powder that doesn't work. While this cup would actually screw right onto our gun.
You don't want to do that because the way the gun works, it needs some air in there to move the powder around to mix it. So, what you want to do is pour off about two ounces of powder. But before you do that it's always a good idea to put on a respirator. In this case, a dust respirator. Just because it is still, it can still go airborne and you don't want to be breathing in powder.
Okay. Now that we have a couple ounces of powder out of the big container and into the gun, the container that'll actually screw to the gun. We can just go ahead and attach that to the gun. Okay. Things to keep in mind with the gun.
It has on the end here. A diverter. And what this does is if you're powder coating a really large part, it forces the powder out into a bigger fan spray. Because our part really isn't that big, we're going to take that off for this. Now, remember this is high voltage.
Once we powered up. This will have a charge to it. So you don't want to touch the end of this. Nor do you want this electrode to touch the part that we're working on because it will arc. Okay.
Now that we have the powder attached, we'll set our pressure to approximately between six and eight pounds. And it's not a lot. Test that. Make sure we have the powder coming out. And we're ready to get our system electrified and start spraying.
Okay, we're going to start the process by actually spraying into some of these crevasse areas. Where I know we're going to get some of that Faraday effect. The Faraday effect is when we build that magnetic shield that we actually prevent powder from going in. On the other, on the backside here. I'm going to go in and spray into this area here.
Just because I want to make sure I get those areas good coverage. Before I start putting an electrical charge into the whole object. And with that, we'll get started. Now that we have all the powder on our piece where it's time to actually bake this. What we don't want to do is touch it at this point.
If we do it'll knock the powder off the piece. If you do accidentally knock the powder off the piece it's not a big deal. All you have to do is simply go back and reapply the powder. We'll set our oven to 400 degrees. We're going to set it for like 50 minutes because it'll take about 10 minutes for it to get hot.
And it's going to take about 40 minutes for it to actually bake. It's going to take a lot longer for the cast iron actually heat up to temperature. And get the bonding and cross-linking that we need in the powder to actually have a good final finish. So with that, we'll let it bake for a while and ready to look at our part. Wow, Mark!
This looks fantastic. Yeah, it really does. This'll look good hanging off the firewall as opposed to the rusty chunk of iron down the road. Well, now that you showed us how easy the process is to powder-coat. Can you talk a little bit of how easy cleanup is?
Cleanup is a breeze. You know. That's the one thing that I love about powder coating. You know, you've noticed I've done all this right next to a fully painted car. We haven't covered the car or anything else.
Because the powder does not stick to anything. And you know, it takes 400 plus degrees heat to actually get it to set. So it's the kind of thing where you can do it in the shop. Without ruining everything else in your shop like painting. And to actually clean it up.
It's a pretty straightforward process. Take off the canister that you've used with your powder and return any unused powder to the original canister. Then rest of the cleanup, both cleaning the gun and cleaning up the canister, we will just be using a compressed air. And it's just a matter of spraying everything out and it will be ready to go for the next round. And any dust that's left around on the shop floor or anywhere else in the shop it's just a matter of sweeping it up.
Because it's just, it's just dry powder at this point. Wow. That was easy. Thanks Mark. for showing us the powder coating kit today.
If you need any more information on Eastwood and all the products they offer car enthusiasts, check out eastwood.com.
When powder coating the master cylinder do you have to take out the rubber seals in the cylinder before baking?
I have the same system from Eastwood. I've had good results thus far. Bought a 30" wall mount oven for the shop. For the most part, if you can fit it in the oven without knocking off the powder you're all set. Each powder has instructions for baking, so far the powder I'm using requires 450 for 10 minutes then 400 for 20 minutes. If a part is heavy, at the end of the baking time I will turn off the oven and leave it in to cool.
Nice video but how do you know how long to leave the part in the oven? thinner pieces compared to heavier ones, does the part need to come up to a certain temp.?