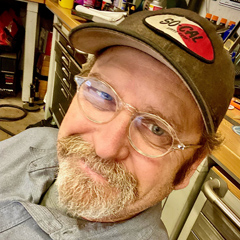
Spot Welder Setup and Safety Tips
Mark SimpsonDescription
Any well-equipped, you know restoration shop or even your home shop, you know has a spot welder. You know it's not a tool you're gonna use every day. It's mainly for joining two pieces of sheet metal together. The advantage of it is unlike using you know, drilling holes and plug welding. You can like join two pieces of metal together, relatively efficiently with, without disturbing the metal a lot.
But the key to really having success with one of these is to properly prepare your metal. So let's take a look at that. You know I've got a couple of pieces of sheet metal here is 18 gauge that we're gonna join using the spot welder, but, in while we've got it formed up, we next need to actually, because there's a little bit of mill scale, any, any anytime metal is formed or made, there's a little bit of mill scale on there. Plus there's some oils from both, you know our hands, as well as, you know when it comes out of the factory, they put a little bit of oil on stuff to keep it from rusting. So the first thing we'll do is actually just wipe the, get the oil, off the metal.
We'll just use a little bit of lacquer thinner on a rag to clean the surface well. You know lacquer thinner will cut the oils and eliminate those the reason you wanna do this before you sand it is you don't wanna like start sanding and sand oils into the metal further. You wanna just kind of get those off the surface. Next, we're going to you know use the just a d a little small d a with some 180 grit paper on it. And we wanna actually sand the areas that are primarily what we wanna do Is sand the areas that are going to be joined together.
What we wanna do is make sure we get a good weld and that includes making sure the metal surfaces can be joined without that mill scale. And it's a good idea to sand the backside too, just because we're relying on an electrical contact between the two, these two probes to actually make the metal between them molten. So if we have a good connection on both the top and the bottom. It'll help us achieve a better spot. You know I can't stress enough the importance of getting a, get rid of the mill scale and cleaning the two pieces of metal because generally that's most spot welds fail is not doing enough prep, to make sure you have a good bond.
After we have our metal cleaned and we've eliminated the mill scale, go ahead and put some clamps somewhere on it to hold it in position. And you're ready to start spot welding. Okay, this spot welder, it's basically a home unit. You know i this was purchased for, you know under a couple hundred bucks and, you have, two electrical probes. Have a handle, that's gonna force them together and then a switch to actually turn on the juice.
And you can see, you know it, it, it, I can tell you this metal is really hot right now, but also it's contained the whole welding process to a single spot henceforth, the named spot weld. And you know by putting a, you know a couple of spot welds in here, we'll be able to hold these two pieces of metal together. Now we've got, In just a matter of moments, we've you know taken this and attach these two panels together. You know this way, we can use this process to build brackets. We can use it to build, patch panels and those difficult areas on a car where you're, you know you need to fabricate something like this and a simple easy, all welded together, ready to go.
Share tips, start a discussion or ask other students a question. If you have a question for the instructor, please click here.
Already a member? Sign in
No Responses to “Spot Welder Setup and Safety Tips”