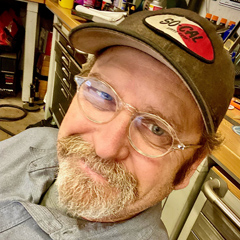
Standard vs Impact Sockets
Mark SimpsonDescription
Material and Construction: Impact sockets and standard sockets differ primarily in material composition and design. Impact sockets are made from more durable, high-strength steel alloys (like chrome molybdenum), which can withstand repeated high-torque impacts. Standard sockets, typically made from chrome vanadium steel, are designed for hand tools that do not apply sudden forces. Impact sockets also have a black oxide coating to prevent corrosion and reduce wear, while standard sockets usually feature a polished chrome finish for appearance and ease of cleaning.
Wall Thickness: Impact sockets generally have thicker walls compared to standard sockets. This added material gives them more strength to absorb the shock from an impact wrench or driver, preventing them from cracking or breaking under stress. In contrast, standard sockets have thinner walls because they are designed for manual use, where sudden, high-impact force isn’t a concern.
Design Features: The interior of impact sockets is typically more rounded or chamfered, which allows them to fit snugly on the fastener while preventing rounding of corners. Standard sockets often have sharper edges, which can wear down fasteners over time. Additionally, impact sockets often feature a hole or groove for a retaining pin to securely attach to power tools, a feature absent from standard sockets.
Benefits and Uses
Impact Sockets
Durability and Safety: Built to withstand the extreme forces of power tools, they reduce the risk of shattering and ensure user safety.
Heavy-Duty Applications: Commonly used with impact wrenches and drivers in automotive repair, heavy machinery maintenance, and industrial environments. They are ideal for removing rusted, stubborn bolts or high-torque situations.
Longevity: Less prone to deformation or wear, making them ideal for regular professional use under tough conditions.
Standard Sockets
Precision and Versatility: Designed for hand tools like ratchets, these are ideal for situations requiring controlled torque and precision, such as in light automotive tasks, household repairs, and general DIY.
Lighter and Easier to Handle: Due to their thinner walls and lighter material, standard sockets are more comfortable for extended manual use.
Impact sockets excel in high-torque, impact-driven environments, offering superior strength and safety, while standard sockets are perfect for precision and manual tasks. The choice between them depends on the application and tool being used.
Share tips, start a discussion or ask other students a question. If you have a question for the instructor, please click here.
Already a member? Sign in
No Responses to “Standard vs Impact Sockets”