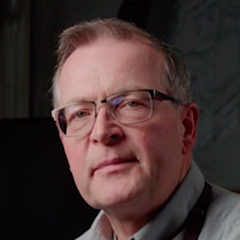
TIG Welding Aluminum Alloy
Bruce MacleodDescription
In most cases, TIG welds hold up well to hammering and fabrication of the metal after welding where some other types of welding can be prone to fatigue or cracking. Another great benefit to TIG welding over other types of welding is how quickly and simply you can switch from welding steel to stainless to aluminum or even perform less-common welding like tungsten or bronze. Aluminum welding can be one of the trickier metals to weld as the weld pool can become easily contaminated, resulting in poor-quality welds.
To gain some insight into TIG welding aluminum and aluminum alloy, we join Bruce Macleod of the Contour Autocraft Academy, who shares some of his 40+ years of experience welding and fabricating aluminum for classic cars. Macleod emphasizes the goal is to create a seamless body panel once complete, and using a TIG welder allows you to create panels that would be impossible to fabricate from a single piece of metal. He also explains the safety items and processes that should be used while TIG welding as well as the basic equipment you’ll need to be successful. Bruce explains the proper setup of the torch, welder settings, and the need for aluminum to be welded with AC current.
Welding aluminum is as much a process as it is a skill, and any skill takes time and practice to perform well, Macleod explains. Comfortable welding positions and repeating the same techniques every time is key to creating repeatable high-quality results. For this demonstration, Bruce shows us how to fuse two panels together without the use of a fill rod and to achieve a finished weld that is the same thickness as the surrounding metal. He also demonstrates the use of a hammer and dolly to stretch the metal back out and flatten the weld, matching the thickness of the base metal. We’re confident that learning this important skill will improve the quality of your restorations.