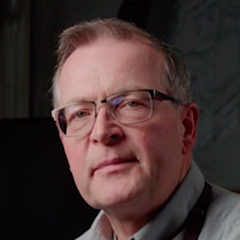
Wire Edge Panel Forming
Bruce MacleodDescription
The primary purpose of wire edge forming is to enhance the structural integrity and aesthetics of automotive sheet metal panels, particularly those used in the construction of vehicle bodies. You’ll commonly see wired edges on fenders and hood sides of 1930s cars and earlier, but occasionally it is used on newer models as well.
When building patch panels for these early cars it is common to have to recreate the wired edge. The process involves folding or bending the edge of a metal panel over a wire to create a secure, strong and finished edge. This wired edge helps to reinforce the panel, provide stiffness, and prevent sharp edges that could cause injury during vehicle assembly or use.
In traditional wire edge forming methods, a wire or metal strip is placed along the edge of the sheet metal panel. The panel is then folded over the wire, creating a double-layered edge. The wire or metal strip acts as a reinforcement and helps to maintain the shape of the fold. Various tools and machinery can be used to achieve the desired edge.
We join Bruce Macleod of the Contour Autocraft Academy to demonstrate the process of forming a wired edge on sheet metal. Macleod discusses what tools and equipment you’ll need to properly form a wired edge, then demonstrates the correct technique to bend the wire and form the wired edge on a sheet metal panel.
Overall, wire edge forming has played a significant role in the automotive industry by enabling the production of structurally sound and visually appealing sheet metal panels.